ONE-MA3 – Creating Strong and Sustainable Mortars
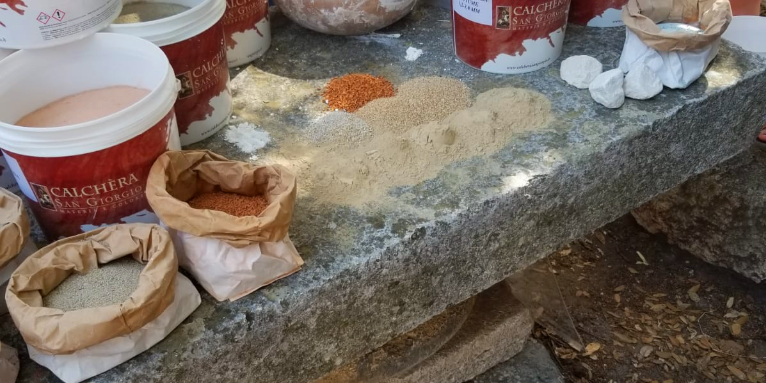
By Naomi Lutz ’22
This morning we had the opportunity to learn about the process of making Roman mortars and the different materials used in them. Then we put our knowledge to the test and made our own mortars! We broke into four groups to come up with our own recipes, and compete to make the strongest, most sustainable mortar.
Professor Masic teaching us about the production of Roman concrete
In thinking about what ingredients to use for our mortar, we compared reactivities, carbon footprints, and strengths of the different materials. A higher reactivity means a stronger mortar, as more chemical bonds must then be broken in order to break the mortar. Unfortunately, some materials with higher reactivities must be heated up to be used, releasing carbon dioxide into the air. Metacaolino has a reactivity of 98% but must be heated to 600-800 degrees. In choosing to include Metacaolino in our mortar, my group thus sacrificed part of our mortar’s sustainability in return for strength and sturdiness. Sturdiness allows infrastructure to last longer and requires less maintenance, making the mortar more sustainable at the same time. Pozzolana, or volcanic ash, on the other hand has a reactivity of 70% and doesn’t need to be heated. Due to these promising characteristics, we chose to use a lot of pozzolana in our recipe. Pozzolana can be found in many parts of Italy, so we mostly used the one from the closest city Tivoli in order to limit the number of miles it was transported, and thus the carbon footprint. It is also purple, giving our mortar a colorful tint. When choosing whether to use pomice or sand, we noted first that pomice is light and has a reactivity of 20%, while sand is heavy and is inert. However, sand is strong and found everywhere and is thus very sustainable. After getting more advice from our TA Janille Maragh, we decided to prioritize using sand in our mortar.
Materials for making mortar
After finally deciding on our recipe, we mixed our ingredients together in a bucket. We then added lime and water while mixing the solution. When we reached a good consistency, we scraped the mortar into plastic cups and shook them in order to reduce the amount air bubbles so that more reactions could occur and therefore increase the strength of our mortar. In a few days, after our sample hardens, Admir and the TAs will judge which mortar is both the strongest and the most sustainable. We can’t wait to see which one wins!
A sample of mortar created from various material
Share on Bluesky